Specialized Storage Buildings
Our specialized storage buildings are 100% customizable and provide the same attention to detail and quality manufacturing processes that U.S. Chemical Storage has become known for.
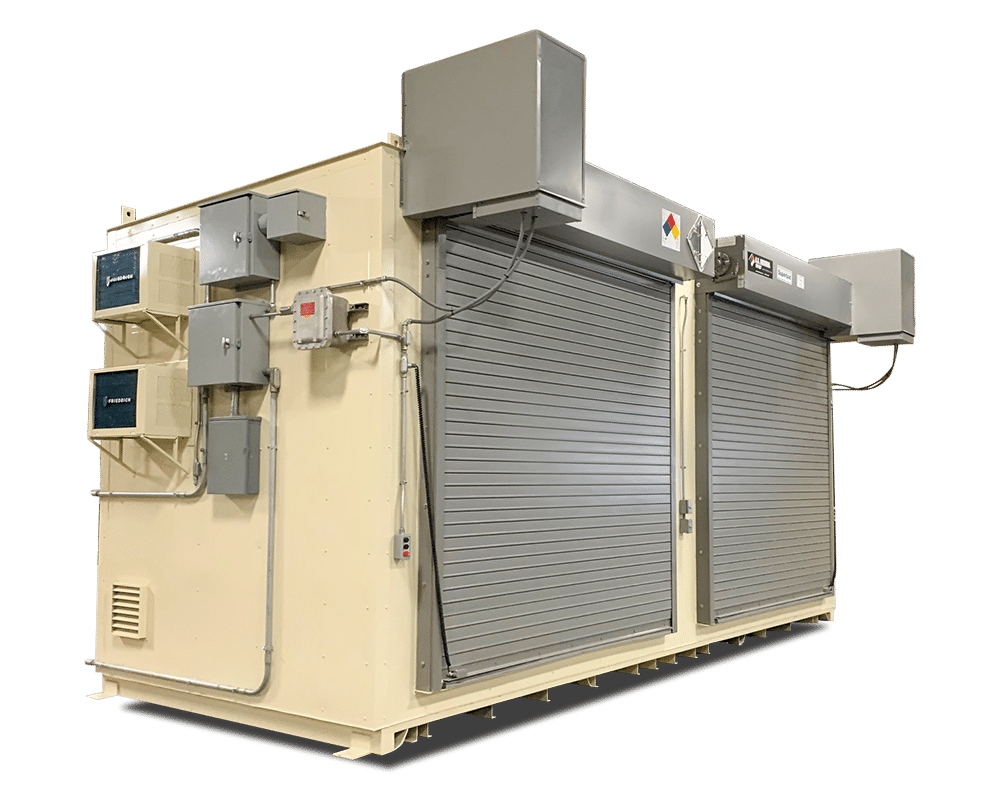
*SuperLocTM storage building
Fully Customizable For Your Unique Application
- 100% customizable
- Alarms, Gas Sensors, Thermostats, Strobes
- Safety Showers and Eyewash Stations
- Fume Hoods & Snorkles
- Flooring Options
- Static Grounding and Buss Bars
- Drum Lifter Cranes
- Gravity Fed Rollers
- Cylinder and Barrel Racks
- Explosion Proof C1D1 and C1D2 options
And much more!
Gas Cylinder Storage Buildings
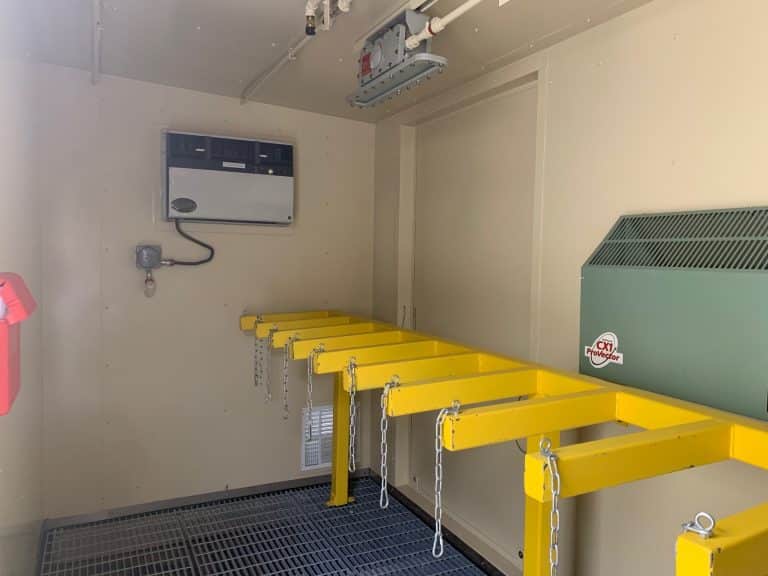
Improper storage of compressed gas cylinders can cause an unsafe work environment. Gas cylinder storage buildings are designed to safely store compressed gases, while increasing operational efficiencies for your manufacturing processes by keeping your compressed gases nearby or even inside your facility.
Choose from fire-rated or non-fire-rated construction to maintain and manage your compressed gas cylinders compliantly. Custom fit your gas cylinder storage container with our full line of parts and accessories, including, but not limited to explosion relief panels, cylinder racks, shelving, gas detectors, alarms, sensors, flooring options, forklift entry doors, roll-up doors, mechanical ventilation and more. Our gas cylinder storage buildings are perfect for welding operations as well as other cutting and brazing operations
Laboratories
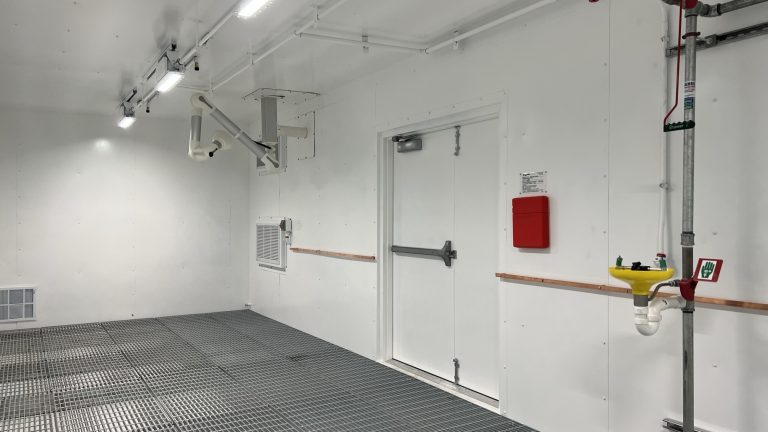
Hazardous conditions and the potential for vandalism make storing and protecting hazardous equipment a necessity. U.S. Chemical Storage’s drop-over hazardous equipment storage buildings are 100% customizable and the most cost-effective option when your valuable equipment requires 24/7 security.
These prefabricated, floorless units are designed to be crane hoisted and lowered over an existing structure to dampen noise, secure existing equipment, and hide unsightly infrastructure components. Regardless of your goal or need, drop-over buildings are the most cost effective solution when there is a pre-existing structure that needs protection.
Multi-Function Storage Buildings
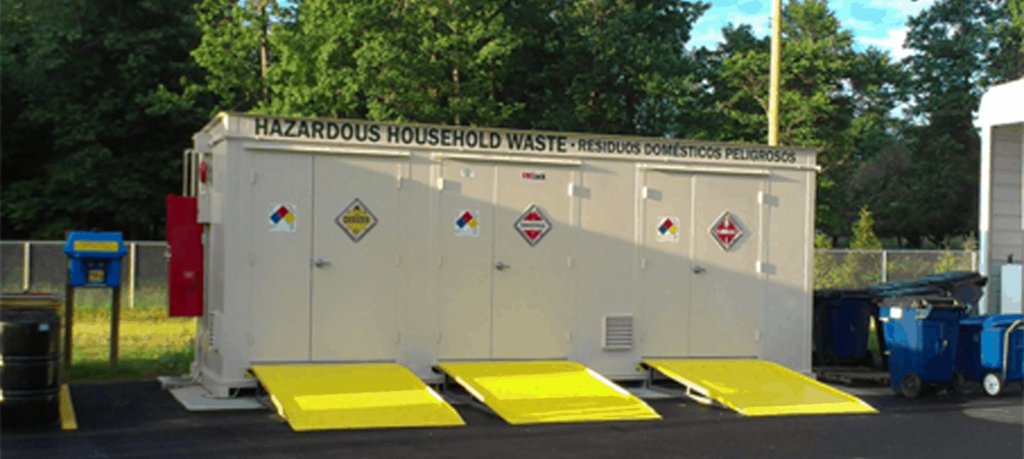
.U.S. Chemical Storage provides multi-compartment hazardous material storage buildings to facilitate safe storage of incompatible materials within the same storage area. Multiple AC, refrigeration, freezer, and heating units can run simultaneously in different compartments in the building to maintain the environment of particular chemical demands. In addition to separate fire suppression and ventilation, our multi-compartment buildings can also feature separate containment sumps to ensure incompatible materials don’t mix from spills, leaks or hazardous accidents.
Additionally, the flexibility of our multi-compartment units allows for a mix of non-explosion proof and explosion proof environments.
Drop-Over Buildings
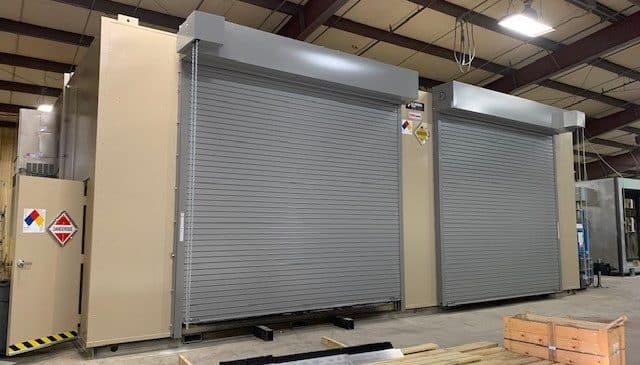
Hazardous conditions and the potential for vandalism make storing and protecting hazardous equipment a necessity. U.S. Chemical Storage’s drop-over hazardous equipment storage buildings, often referred to as “drop over buildings” are 100% customizable and the most cost-effective option when your valuable equipment requires 24/7 security.
These prefabricated, floorless units are designed to be crane hoisted and lowered over an existing structure to dampen noise, secure existing equipment, and hide unsightly infrastructure components. Regardless of your goal or need, drop-over buildings are the most cost effective solution when there is a pre-existing structure that needs protection.
Frequently Asked Questions
The definition of a “sump” is a pit or reservoir providing containment for spilled liquids. U.S. Chemical Storage offers leak-proof spill containment sumps in each standard model. All our sumps are tested for leaks for a 24-hour period prior to finishing. The sump is then covered by a steel or fiberglass floor grating and can even be equipped with a resistant plastic sump liner to protect against corrosive chemical accidental spills. The size of the sump is dictated by code based on the volume of liquid being stored within the building.
Building size is determined by the amount of hazardous material you are planning to store, the need for occupancy or inspection around these materials, and must take into consideration the most efficient way of moving these materials into and out of your chemical storage building.
Start by speaking with one of our experienced Technical Sales Engineers to learn about the needs of your application. They will want to know what type of chemicals you are storing? How much of it will you be storing? What proximity to other buildings, people, egress paths, or environmental features will it need to be? Do you require special spill containment? And from there they’ll ask any related questions that determine additional options; Material Handling – Climate Control – Ventilation – Occupancy – Lights – Sensors – Alarms – Door Styles – Eyewash Stations and other requirements are not uncommon. Answers to these questions will dictate the building’s fire rating construction as well as anything else you’ll need for proper code compliance.
Request a Quote
RELATED PRODUCTS
Ventilation Options for Your Storage Building
Proper chemical storage ventilation within your chemical storage building can maximize worker and environmental safety. View >Partition
Walls
Segregating chemicals with partition walls allows for the storage of multiple chemicals inside the same chemical storage building.
View > ChemLoc™ Chemical Storage Buildings
These chemical storage units have countless applications and accessories that can be custom engineered to fit your specific needs. View >SuperLoc™ Flammable Storage Buildings
4-hour flammable storage buildings ensure compliance while improving efficiency and allow for flammable storage located within 10 feet from and even inside your facility. View >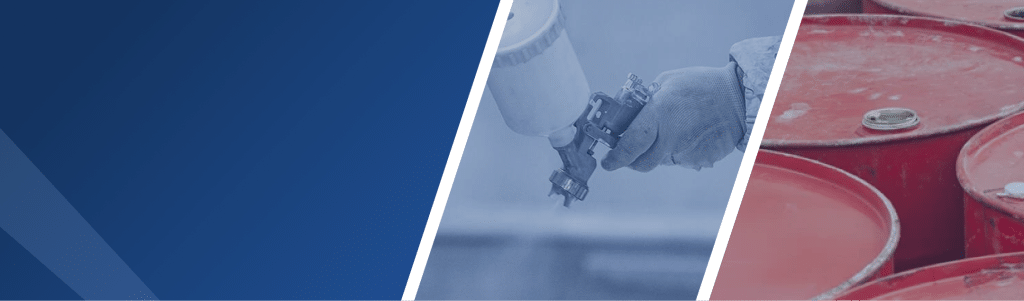
YOUR PARTNER IN THE PROCESS. EXPERIENCE YOU CAN TRUST.
We deliver the precise building solution with the speed, security, and high quality that you demand.